The International Standards Organization (ISO) in Geneva has published the new profile standards ISO 21920-1, -2 and -3 for surface textures with edition 2021-12. They combine the previous surface finish standards into one series of standards. They were initiated by international teams of experts – Mahr GmbH in Göttingen was involved twice at the project manager level.
When you put a sheet of paper in the printer, you don’t think twice about it: The paper size fits the printer, the printer fits the paper. This is no coincidence, but the result of a standard. According to the German Institute for Standardization e. V. (DIN), around 34,000 standards currently make up the German body of standards. They provide manufacturers and consumers with important rules, set standards for products and processes, and create clear criteria – often even worldwide.
The three parts of the new body of standards are an important building block in the international standards concept of Geometric Product Specification (GPS system), which has been developed for almost 25 years. Following on from the already published standards for surface finish specification, the DIN EN ISO 25178 series of standards, DIN EN ISO 21920 also provides an updated version of the relevant profile standards. The previous profile standards
- ISO 4287:1997-04 “Parameters”
- ISO 4288:1996-08 “Measurement conditions”
- ISO 13565-1 to 3 “Load-bearing component”
- ISO 1302:2002-02 “Drawing entries”
are being withdrawn. “They no longer cover all the possibilities of modern measuring instruments – for example, because they did not offer standardized procedures for optical measuring instruments to date. In addition, they did not always correspond to current industrial practice and in some cases had fuzziness in the definition of some parameter algorithms,” explains Heinz-Joachim Kedziora, Head of Surface Metrology Development at Mahr. He is also the project manager responsible for the third part of the new standard internationally and has also taken on this task for the first part of the standard in the summer of 2021. “DIN EN ISO 12085 (“Motif”) will remain; the revision of DIN EN ISO 3274 (“Stylus”) has been started in the meantime.”
Update and optimization
For historical reasons, some of the previous standards had quite different numbers. They ranged from “ISO 3274:1996-12 Measuring instruments” to “ISO 4287:1997-04 Parameters” and “ISO 4288:1996-08 Measurement conditions” – just to name a few. From now on, they will be summarized in the new DIN ISO 21920. It thus maps the entire process – from design to production to quality control 0 in three parts. Thus, the first part (ISO 21920-1) deals with manufacturing and specification, i.e. “drawing entries”. Part 2 (ISO 21920-2) defines the parameters, and Part 3 (ISO 21920-3) formulates the conditions for checking these parameters at the end.
Part 1: Drawing ensures functions of the component
Part 1 replaces the previous ISO 1302 and covers the processes surrounding the drawing entries that a designer specifies for the manufacture of a component. The most important change: from now on, only the drawing is the basis for the conditions used to check a manufactured component. “Even if a designer develops something particularly complicated, Part 1 defines how he must specify the part without adding free text. In this way, it is possible that the specification alone ensures the function of the component,” explains Heinz-Joachim Kedziora. Example: So if you only specify the parameter “Ra” and a value, then in many cases it is not ensured that this specification correlates with the functional behavior of the part. Here, there are more complex and less complex parameters. In addition, Part 1 includes new terms for the surface parameters:
Term | Abbreviation | Explanation |
Evaluation length | le | “evaluation length”, the part of the sensing distance that is evaluated; replaces lmor ln. |
Nesting index | Nic, Nis | “cutoff wavelength” only useful for linear filters; replaces λc and λs. |
Profile S filter | Profile-S filter removes short wavelength components (low pass); for roughness parameters, the Nis filter(“λs filter”) removes very short wavelength components that do not belong to the R profile. For ripple parameters, theNic filter(“λc-filter”) removes short-wave components that belong to the R-profile and not to the W-profile. | |
Profile L filter | Profile L filter removes long-wave components (high-pass); for roughness parameters, theNic filter(“λc filter”) removes long-wave components that do not belong to the R profile. | |
Section length | lsc | “section length” for the parameters calculated from profile sections, e.g. Rz, Rp, Rv; replaces the term “single measurement section”. |
Number of sections | nsc | “number of sections”; replaces the term “number of individual measured sections |
Important for all users: The new standard applies only to new drawings. Older dated drawings retain their validity under the previous standard.
Also new are some symbols introduced to establish the clear reference of a drawing according to DIN EN ISO 21920-1:

Part 2: Designers are in demand
The second part of the new ISO 21920 deals with the relationship between parameters and functions of components. It is the most comprehensive and probably most difficult part and replaces the former ISO 4287. “More than 100 parameters are described here, offering designers an enormous toolbox. In the future, they will be asked to select the right parameter from this part. Experience has shown that many users find the selection difficult, as this topic is not a training focus,” says the development manager.
In the case of the parameters calculated from profile elements (= a mountain and a valley in the profile), there were previously greater measurement uncertainties because the profile elements were described but not clearly defined in detail, especially in borderline cases. This has now been significantly improved. However, metrology manufacturers are not forced to program all these parameters into a device or software, since some of them only play a role regionally.
Part 3: How to arrive at a valid result
Part 3 defines the conditions according to or under which measurements are made. It replaces the previous ISO 4288 and deals with the subject of “Specification and Verification” – i.e. requirements for measurement procedures and their correct implementation. Part 3thus defines the default case. This means that if no explicit specifications are made in the drawing, what is in the standard applies – in other words, everything that does not have to be explicitly specified.
“So this part is not only about the measurement conditions, but also about additional factors to be taken into account, how to get a valid result. Therefore, there are no prescriptions in this part on how to measure something, but only the description of a complete specification operator,” Kedziora explains. The specification is theoretically ideal and unambiguous. According to ISO 8015, “The verification operator is the physical implementation of the specification operator. It can have exactly the same operations in the same order (in which case the procedural uncertainty is zero) or it can have different operations or perform the operations in a different order (in which case the procedural uncertainty is not zero).”
For verification, therefore, one simply specifies the uncertainty, which is not easy in practice for the most part. As an example, consider the use of the Gaussian filter: If in the standard case the specification assumes a profile point spacing of 0.5 µm, it is not forbidden to use a larger or smaller point spacing during verification; the user must then take this into account when estimating the measurement uncertainty.
Conclusion: Expanded possibilities for function descriptions
For most users, the new standard changes nothing at all. It only offers extended possibilities for functional descriptions, for example in additive manufacturing processes, where new structures or new filters are sometimes required.
Unlike in the past, it is no longer the workpiece that determines the filter setting, but the associated drawing. This increases the reliability of the decision as to whether the tested surface meets the requirements or not. There is no longer any need for the time-consuming – and in practice hardly observed –procedure according to DIN EN ISO 4288 for inspecting a workpiece surface, including the subjective assessment of whether a profile is periodic or aperiodic.
Overall, great emphasis was placed on continuity in the new standard. “The bottom line is that the weak points of the old standard – such as imprecise and non-practical definitions – have been eliminated. Where the old standard delivered reasonable results, this also applies to the new standard. Where the old standard was fuzzy, the new standard is sharper,” summarizes development manager Kedziora. “Due to the continuity by which the new profile standard retains everything that has proven itself in industrial practice, users can continue to measure in accordance with the standard even with their existing measuring devices.”
Currently, the German Institute for Standardization e. V. (DIN) is drafting the national standards DIN EN ISO 21920-1, -2 and -3. It is strongly recommended that the editions DIN EN ISO 21920-1, -2 and -3, which were published as early drafts as early as 2020, be withdrawn from circulation, as there were still changes in the international discussion leading up to the final version of the series of standards.
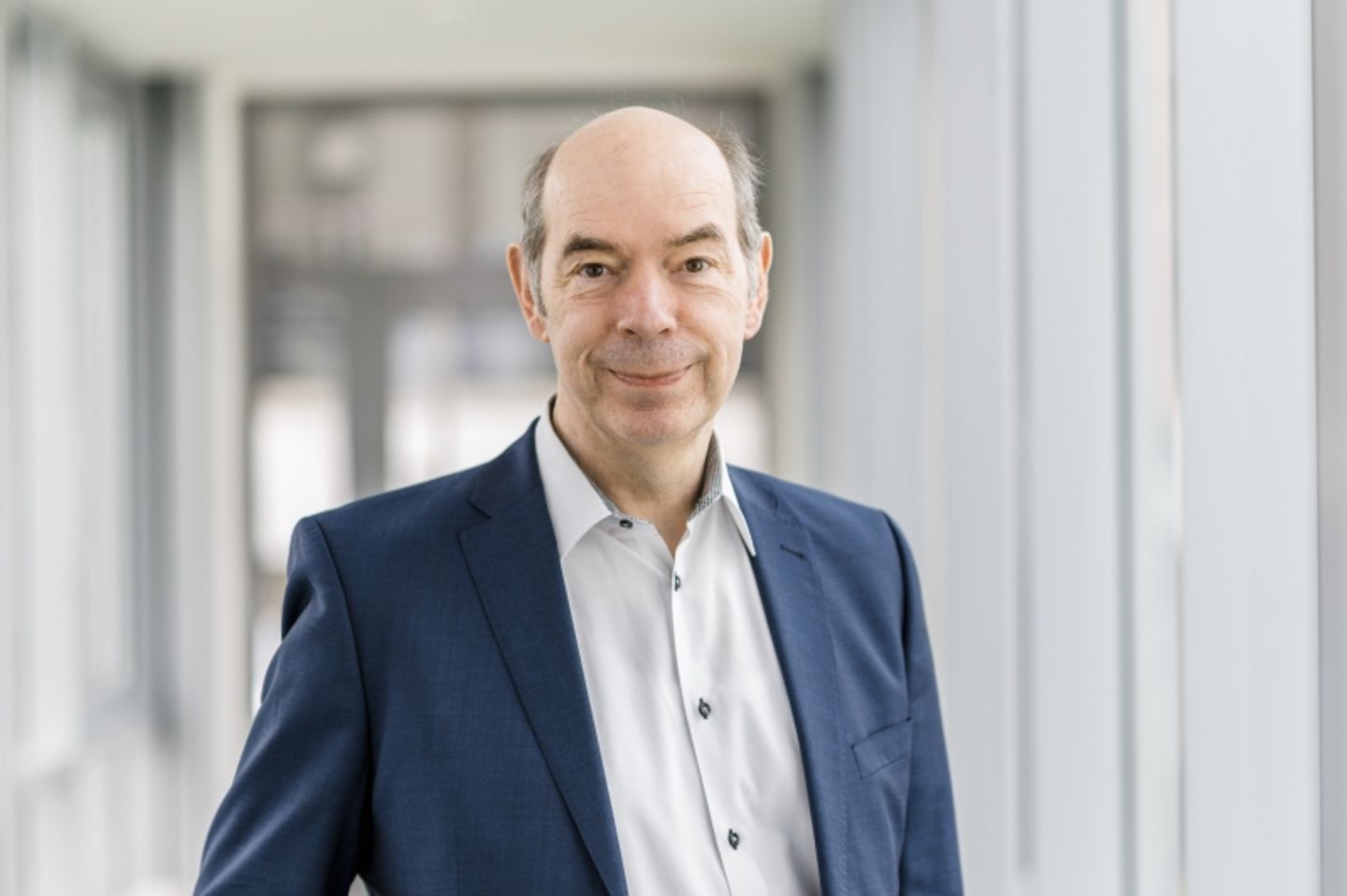
Tip:
Mahr is devoting a comprehensive webinar to the new ISO 21920 under the name “New Surface Standard”. What the new standard has in store for metrologists and users is explained clearly and in detail. > View seminar
The changes at a glance:
- A few new terms
- New symbol for the specification
- The default tolerance acceptance rule is the maximum value rule (“max. rule”).
- The rule values are based on the specification (drawing entry) and not on estimated values of the specified parameter. As a result, the assignment of nesting index is somewhat shifted depending on the specified Ra or Rz value.
- If nothing else is specified, verification is performed at the location of the specified geometry element where the maximum values are expected; imperfections such as scratches or pores must be included.
- No distinction between periodic and aperiodic profiles
- Parameters are (with a few exceptions) defined by the evaluation section.
- Only a few parameters, e.g. Rz, Rp, Rv are defined via profile sections (the term “sampling length” or “single measuring section” is no longer used).
- The specification of the tolerance limit follows immediately after the parameter designation.
- Simplified notation for the specification of bilateral tolerance limits
- A third tolerance acceptance rule: “Tmed”: The median value of all measured values must lie within the specified tolerance limits.
- The specification of optical methods for profile acquisition is possible, e.g. EP OR(1).
This content was first published on the Mahr website.